1引 言
工业生产过程参数如温度,压力等检测中以流量和各相持率测量为复杂是较难测量的两个参数因而引起了工程技术人员的兴趣-随着工业的发展被测对象不再限于单相而要对多相流,混合状态的流量进行测量-测量多相流的技术难度要比单相流体的精确测量大得多知道单相流体的密度,粘度及测量装置的几何结构 便可以对单相流进行定量分析-如果能利用多相流中每一相的上述革理量对多相流进行测量得话就很方便-但遗憾的是多相流体的特性远比单相流体的特性复杂得多如各组分之间不能均匀混合,混合流体的异常性,流型转变相对速度,流体性质,管道结构,流动方向等因素将导致涡轮流量传感器响应特性的改变.
涡轮流量传感器和显示仪表组成的液体涡轮流量计以良好的重复性,宽广的线性工作区和高精度而受到用户的欢迎.液体涡轮流量计在测量单相时工兹定性较 好但在多相流动时由于各相的速度,粘度,局部持率等因素影响涡轮转速-按常规同一流量所对应的涡轮转速保持不变即仪器常数不变-但在多相流动时即使在总流量保持不变的情况下混合流体的密度发生变化也会引起涡轮转速的很大变化-由于在多相流动中涡轮响应特性发生了变化目前面临的问题是涡轮流量传感器是否能成功地应用于多相流的测量及如何设计用于多相流测量的涡轮流量传感器-就此问题 这里首先对涡轮传感器进行了理论分析然后给出三相流动中液体涡轮流量计的实验响应特性后总结出用液体涡轮流量计测量多相流流量的半理论半经验公式
2.液体涡轮流量计测量原理
2.1流量计的响应方程
液体涡轮流量计通过涡轮转数反映被测流量的大小涡轮转数N与流量Q之间的关系可以表示为N=K(Q-q)
式中:K-仪表常数
q-启动流量通过标定获得
2.2液体涡轮流量计固有仪表常数的理论计算
液体涡轮流量计固有仪表常数K0主要与涡轮传感器 结构参数有关 图(1), K0可按下式计算
式2可见,对确定的涡轮流量传感器)易知口径D大, K0值小,叶片数n大, K0值大等.如果要获得较大的仪表常数,就要对涡轮传感器的结构参数进行优化设计,从图2(可以看出,叶片高度;增加, K0增大,导程角增大, K0增大.对于¢19的过环空大排量液体涡轮流量计而言,由上式计算得K0=74.567rpm/m3/d而水中标定的KW=78.89rpm/m3/d,表1给出不同口径和不同导程角下液体涡轮流量计固有仪表常数的计算值.
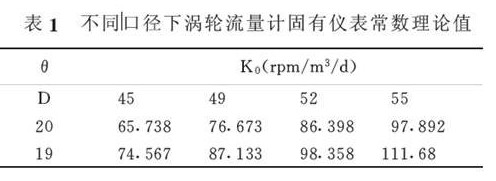
3.液体涡轮流量计在多相流中的响应实验
实验在以空气、柴油和水为介质的三相流动模拟装置中进行,透明的井筒内径为125mm流体全部集流后进入流量计,实验发现,总流量相等,但流动密度不等的实验, K0值变化较大;流动密度相等,总流量不等的实验, K0值变化较小图(3).多相流动中涡轮仪器常数校正因子CK与流动密度Pn之间的统计关系为CK=Pn 0.5次方
4.多相流流量测量
由于机械加工及安装工艺等方面的原因,按液体涡轮流量计固有仪表常数设计的涡轮,必须在水中标定后才能使用,设水中标定的涡轮仪表常数为kw则通过上述理论计算和实验,归纳总结出液体涡轮流量计在多相流动中的响应方程为:
Q=N/K+q
K=KW+K0(Pn 0.5次方-1_
式中kVV为水中标定的仪表常数
如果用全集流型液体涡轮流量计测得涡轮转数N,在标准计量装置上通过标定获得kw和q结合辅助参数Pn就可以用公式(3)计算出多相流总量.用(3)式在油井的油、气、水多相流流量测量中得到了实际应用,计算误差在5%以内。
5.结论
通过理论计算和多相流实验)总结出了液体涡轮流量计仪器常数在多相流动中的实验关系)结合理论和实验)给出了用液体涡轮流量计测量多相流总流量的半经验半理论关系式)实际应用证明该方法可行。
本文由管道式电磁流量计,西安仕乐克涡街流量计厂为您提供,转载请注明出处!!